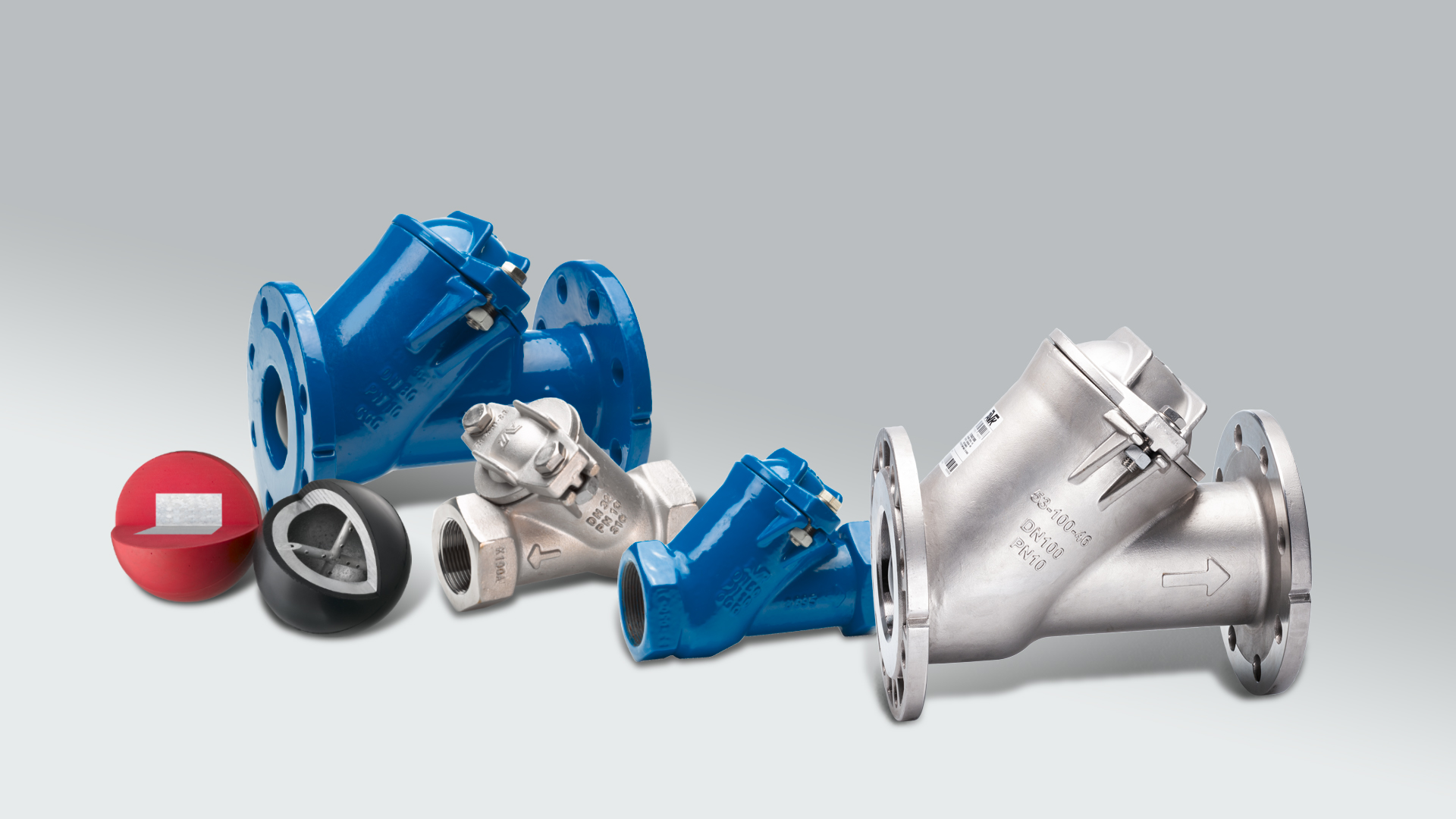
Ball check valves
AVK offers ball check valves in DN32-DN600 with polyurethane balls for abrasive media or with NBR lined balls as standard. They can be mounted in a vertical or horizontal position.
What is a ball check valve?
A ball that travels up and down inside the valve is how a ball check valve works. The seat is machined to suit the ball, and the chamber is cynically designed to direct the ball into the seat to seal and block a reverse flow.
A heavier ball can be used to prevent water hammer from occurring when the pump stops, while a lighter ball can be used if the pump capacity is insufficient.
Where do we use a ball check valve?
Ball check valves are frequently installed on the outlet side of the pumps to safeguard them against damage. Their purpose in a pipeline system is to prevent backflow. Ball check valves are frequently utilized in irrigation, fire safety, and wastewater applications.
Ball check valves require minimal maintenance and can be used in pumping stations with limited supervision, usually if the ball makes noise caused by insufficient pump capacity or water hammer.
AVK Ball Check valves are available with internal thread Series 53/30 DN32-DN50 and with flanges series 53/35 in DN50-DN600. The basic valve design ensures easy maintenance, cost effective operation, and has long life.
The design features 100% free flow, as the ball is completely out of the valve flow path when in the fully open position.
The straight bore prevents deposits in the valve, as all impurities can pass through the valve. Consequently, the AVK ball check valves feature very low head loss giving the benefits of optimum use of pump capacity. Great installation flexibility is another essential benefit of the unique valve design. The valve can be installed both vertically and horizontally as the valve body locates the ball against the seat in either valve position.
Based on AVK’s experience within the sewage treatment sector the materials selected ensure long life and optimum function under a wide range of working conditions.
The body and bonnet are made of Ductile Iron with electrostatically applied epoxy coating internally and externally. Thorough control of layer thickness, adhesive strength and impact resistance of the coating is maintained to ensure optimum corrosion protection. The bonnet bolts and nuts are made of Stainless Steel A4 providing high strength and corrosion resistance.
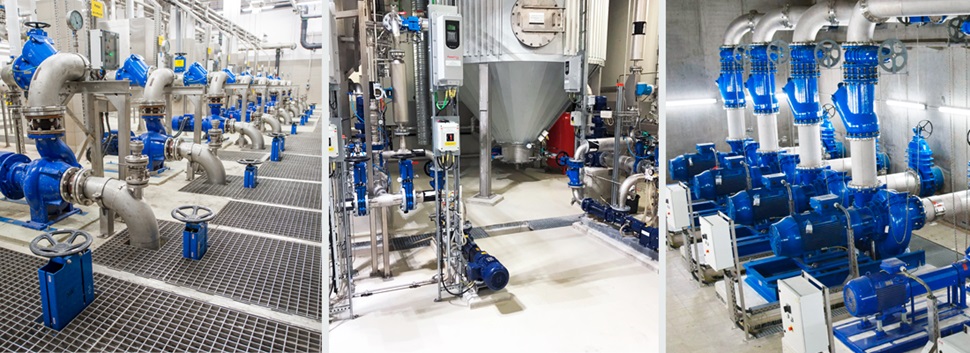