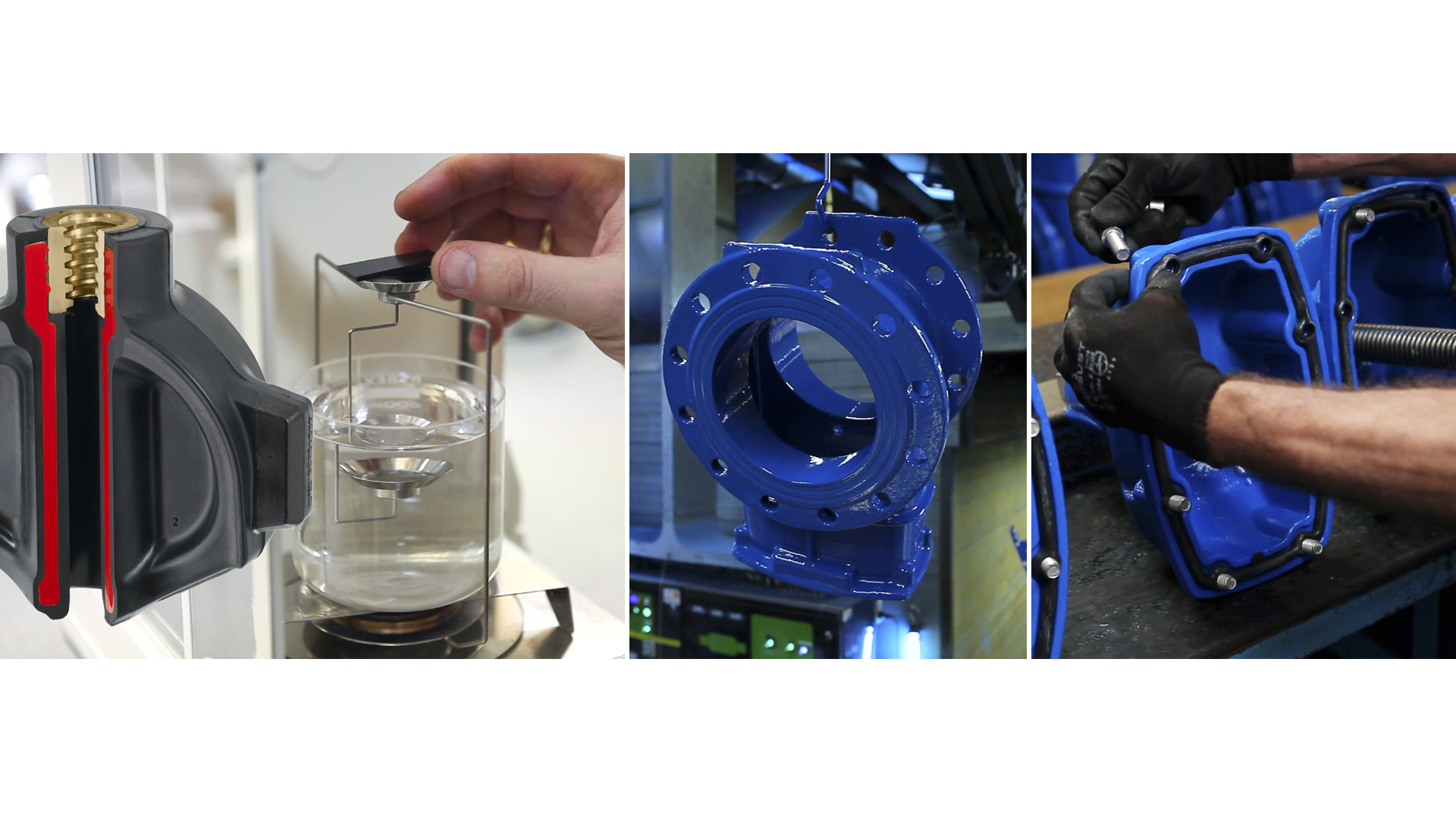
How to choose the right gate valve?
Choose a gate valve with a strong, long-lasting design to save money on replacements. Five fundamentals can help for making the best choice.
1.) The optimal wedge design
The wedge is the sealing part of a gate valve and is therefore crucial. Considering the following:
Different types of wedge nut designs
The wedge nut connects the wedge to the stem. There are two fundamental types of wedge nuts: a fixed wedge nut design, in which the nut is extended in the wedge core, and a loose wedge nut design, in which the brass nut slides in a slot in the wedge core. By reducing the number of moveable parts is reduced, thus eliminating the risk of corrosion as a result of moving parts damaging the rubber surface of the wedge core. A fixed wedge nut design is therefore recommended.
Wedge guides and shoes
When the valve is opened and closed during pipeline operation, the wedge is exposed to stress forces and friction. To prevent the stem from bending downstream as a result of flow velocity, guides in the wedge that fit into matching grooves in the body aid in stabilizing the wedge position during operation. Because of the friction between the wedge and the body’s guiderail, wedge shoes assist prevents the rubber on the wedge surface from wearing through. Make sure that the wedge shoes are fixed and that there is enough rubber underneath to prevent the corrosion of the wedge core.
Rubber
The wedge must be completely vulcanised with rubber for the valve to be tight, and the volume of rubber on the wedge's sealing area must be adequate to absorb contaminants in the seat. To guarantee a proper seal even when the rubber is compressed and to stop creeping corrosion even if a sharp object pierces the rubber during valve closure, a strong bond between the rubber and the wedge core is essential.
2.) Rubber quality - compression set, durability and approvals
The quality of the rubber is essential to both the valve's longevity and operation. In order for the rubber to seal tightly, it must be able to absorb tiny impurities in the seat and endure repeated impacts from chemicals and contaminants without breaking. Consider the following:
Compression set- the ability to regain original shape
The compression set refers to the rubber's capacity to return to its initial form following compression. A higher compression set value improves the rubber's capacity to retain its shape and shut 100% tight year after year, while the EN 681-1 standard specifies the minimum criteria for this number.
How to avoid formation of biofilm
When organic materials left the rubber compound, they serve as nutrients to microorganisms, which begin to develop biofilm and contaminate the drinking water. Choose valves with a wedge rubber that minimizes the amount of biofilm
Resistance to water treatment chemicals
Chlorine and other chemicals are commonly utilized to disinfect old age pipes and clean new ones. Low amounts of chlorine and ozone can also be added to the water to make it drinkable. Because chemical treatment of the drinking water would cause the wedge core to corrode, the rubber compound must not break down or degrade.
Drinking water approval
Every rubber part that meets drinking water needs to be approved for drinking water. The rubber that comes into direct contact with drinking water should have one of the major approvals, such as DVGW/KTW, KIWA, or NF, if no local permissions are needed.
3.) The importance of external corrosion protection
The external corrosion protection is crucial for the service life of the valve. A consistent and even epoxy coating in line with DIN 3476 part 1, EN 14901 and GSK* standards is recommended and involves the following:
Blast cleaning - according to ISO 12944-4.
Layer thickness - Min. 250μm on all areas.
MIBK test - A cross-linkage test (MIBK test) is required to verify that the epoxy coating has cured. On a test piece, one drop of methyl isobutyl ketone is applied. A fresh white cloth is used to cleanse the test area after 30 seconds. The fabric must stay clean, and the test surface cannot get smudged or matted.
Impact resistance - A one-meter-long tube is used to drop a stainless-steel cylinder onto the coated surface. The component must be electrically verified following each collision, and there must be no electrical breakthrough.
Freedom of pores – A 3Kv detector with a brush electrode is used to reveal and locate any pinholes in the coating.
4.) Tight construction
There are two important design issues:
Stem sealing
The bonnet's sealing around the stem keeps the valve or pipeline's internal pressure constant. Stem sealings should always be made to be maintenance-free and last the valve's service life, or at the very least, meet its requirements according to EN 1074-2. It is preferable to design the primary seal that maintains internal pressure as a hydraulic seal, which provides a tighter seal with higher internal pressure. The stem should be surrounded by backup seals. A sealing should be applied around the top stem to shield the sealings from external contamination. Where there is direct contact with drinking water, a high-quality EPDM rubber compound that has been approved for drinking water use must be utilized for safety and health reasons.
Bonnet/body sealing
Using a gasket that is inserted into a valve recess, the bonnet and body can be made tighter. The gasket will stay in its proper position and not blow out due to pressure surges thanks to this design. To protect the bonnet bolts against corrosion the bonnet gasket should encircle the bolts, and the bolts should be embedded in the valve in such a way that no threads are exposed to the surroundings.
5.) General Performance
When operating a gate valve either by handwheel or by means of an electric actuator it is important to pay attention to the operating and closing torque.
Operating torques
Depending on the size of the valve, the torque required to move it from the open to the closed position should range from 5 to 30 Nm. When a valve's operating torque is less than 5 Nm, it encourages the operator to close the valve too quickly, which increases the risk of water hammer and pressure increases in the pipeline.
Closing torques
The torque required to securely close the valve to a drop tight position. For handwheel-operated valves, this torque should be balanced against the handwheel diameter such that the user is not subjected to rim-forces greater than 30–40 kg. The torque should be within the bounds of a normal range actuator when using an electric actuator or a manual gearbox to operate the valve. It is crucial to note that actuators typically have a fairly broad torque range, and the ISO flange connection between the actuator and valve frequently dictates the actuator selection. As a general rule, valves with ISO flange connection should have max. torques for closing as indicated below:
To enable the use of pipe cleaning devices the inside diameter of the valves should correspond to the nominal size of the valve. GSK stands for Gütegemeinshaft Schwerer Korrosionsschutz, and is an independent quality association with about 30 members, all leading European valve and fittings manufacturers. GSK outlines requirements for the coating itself and for the control procedures of the finished coating.